Double station automatic control rotomolding machine for kayak boat
- $18800.00 /set
- 1 set
- Shandong Jinxiu Shanhe Environmental Engineering Co., Ltd.
- Shandong, China
- Ms Jane Wang
Brand Name: | Jinxiushanhe; | Applicable Industries: | Hotels,Garment Shops,Manufacturing Plant,Food & Beverage Factory,Farms,Construction works ,Energy & Mining,Food & Beverage Shops,Advertising Company; |
After-sales Service Provided: | Video technical support,Free spare parts,Field installation, commissioning and training,Field maintenance and repair service,Online support; | Place of Origin: | Shandong, China; |
color: | Blue Green Red Grey etc.; | Certification: | ISO9001:2008; |
Power: | 5500; | Package Preview: | ; |
Port: | Qingdao Port Tianjin Port Shanghai Port; | Warranty: | 1 Year; |
Dimension(L*W*H): | 5m*2m*2m; | Packaging Detail: | Products are tailored to customers, transport, packaging, etc. Several options are available for customers to choose Product LWH reference only not as the actual size, weight according to the size of the material that you use to calculate the actual considerations do; |
customization: | yes; | Voltage: | 380V; |
Automatic grade: | fully automatic; | Weight: | 3000kg; |
Condition: | New; | Payment Terms: | L/C,T/T,Western Union,MoneyGram; |
Supply Ability: | 20 Sets per Month; | MOQ: | 1 set; |
Key Selling Points: | Competitive Price; |
Rotational roto molding plastic water tank machinery PRODUCTION PROCESS

Rotational molding working principle
The unique design of the Roto Molding Machine allows for uniform coating of plastic inside each mould.
Pictured to the right is our Independent Roto Molding Machine. This is one of the most common machines in the industry. It has three arms.
The machine is an independent model. The independent machines are available with up to three arms that can move separately from the others. This allows for different size moulds, with different heating and thickness needs.
It consists of an oven, a cooling chamber, and mould spindles. The spindles are mounted on a rotating axis, which provides a uniform coating of the plastic inside each mould.

otational molding machine ADVANTAGES
:
The rotational molding process offers several advantages. Manufacturing large, hollow parts such as our poly snouts is more easily done by rotational molding than any other method. Rotational moulds are considerably less expensive than other types of moulds. The products can be custom-designed to meet precise market requirements more economically than by conventional injection or blow molding.
Very little material is wasted using this process, and excess material can often be re-used, making it a very economically and environmentally viable manufacturing process. What material is wasted, through scrap or failed part testing, can be recycled.
The process also has fundamental design strengths, such as consistent wall thickness and strong outside corners that are essentially stress free.
rotational molding machine MATERIALS:
More than 80% of all the material used is from the polyethylene family:
Linear low-density polyethylene (LLDPE)-Stocked
Cross-linked polyethylene (PEX)
Low-density polyethylene (LDPE)
High-density polyethylene (HDPE)
Regrind
Other compounds are PVC plastisols, nylons and polypropylene
The order of materials most commonly used by industry is:
Polyethylene
Polypropylene
Polyvinyl chloride
Nylon
Polycarbonate
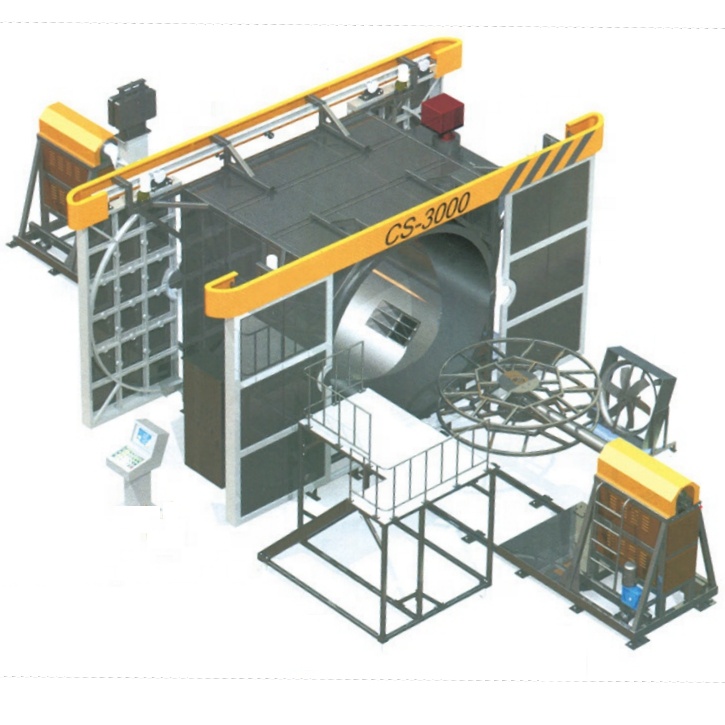
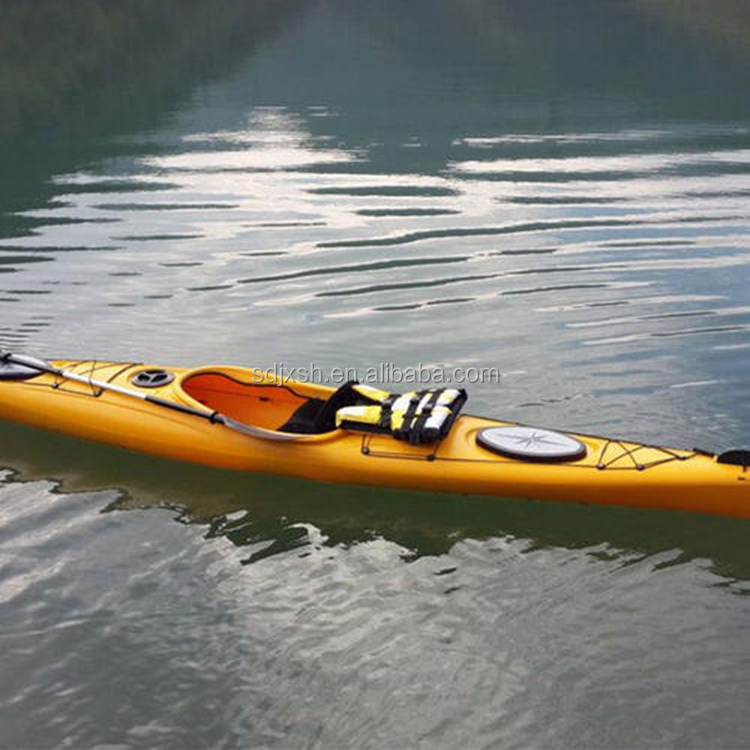
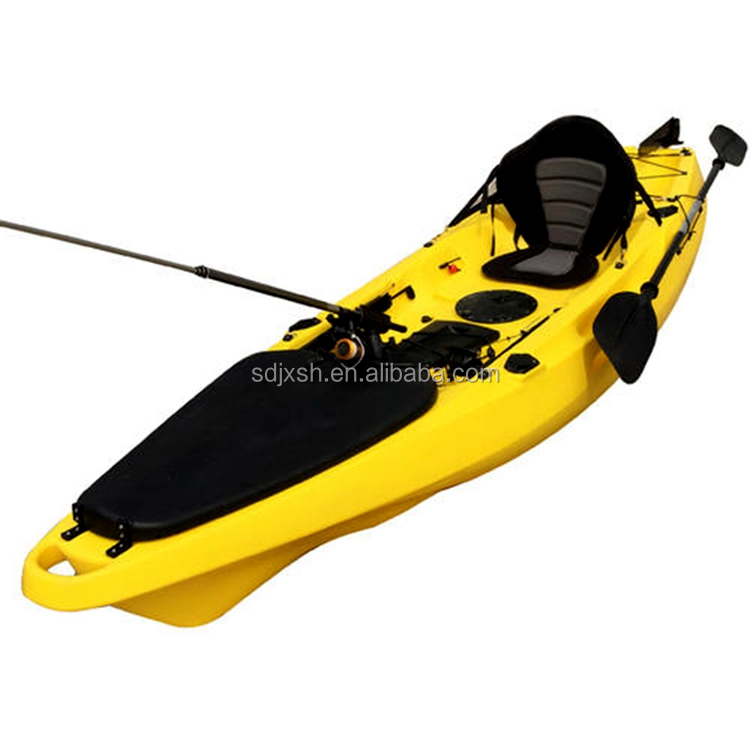
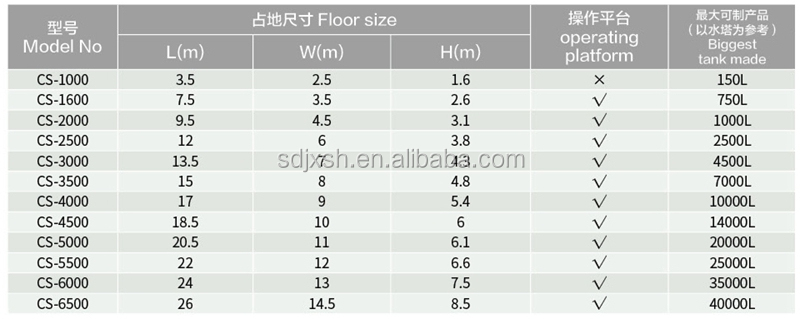
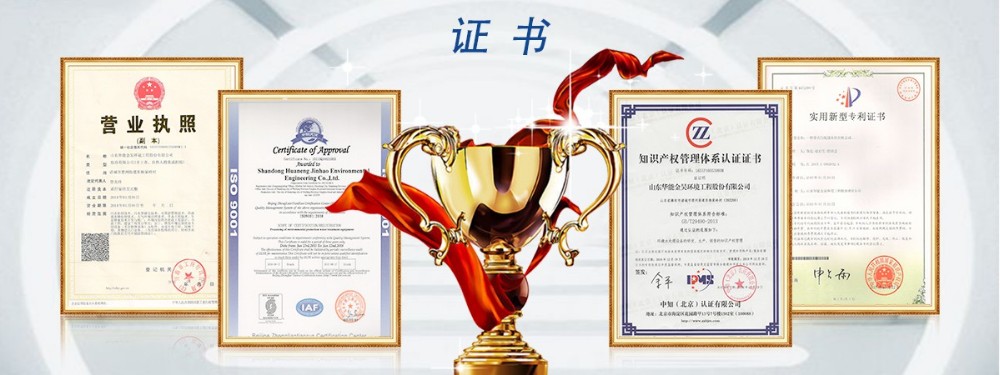

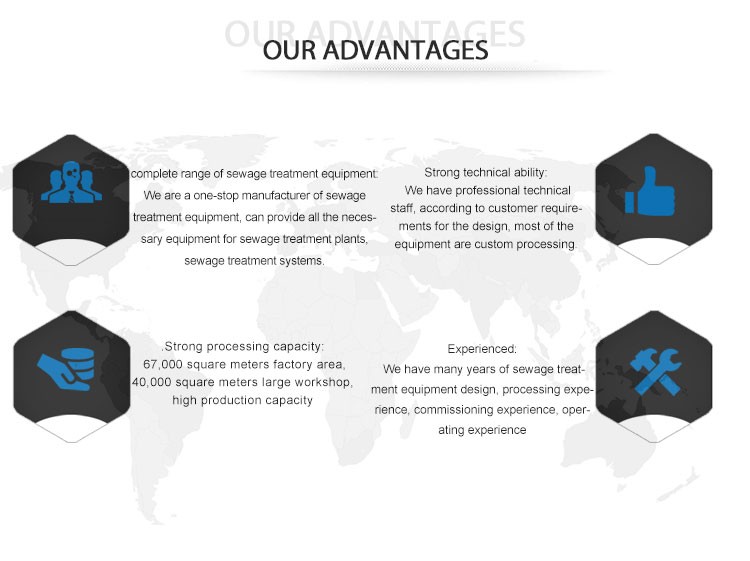
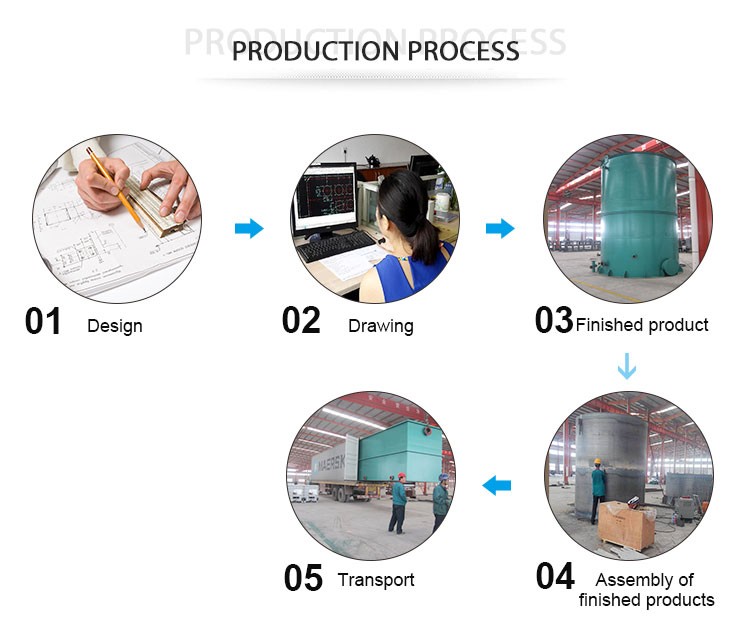
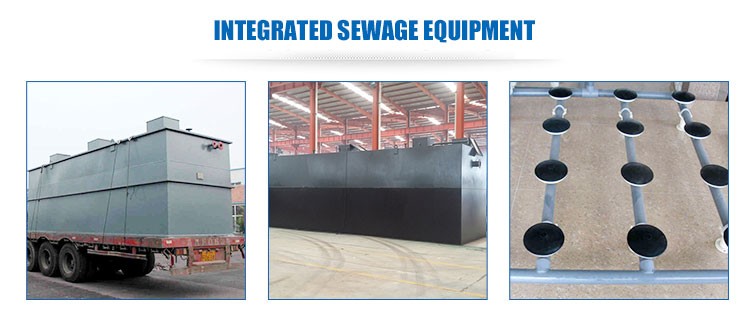
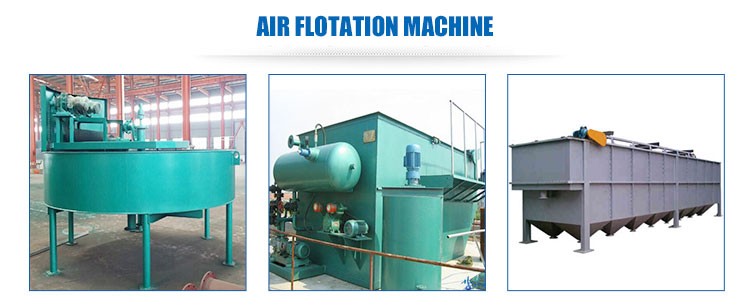
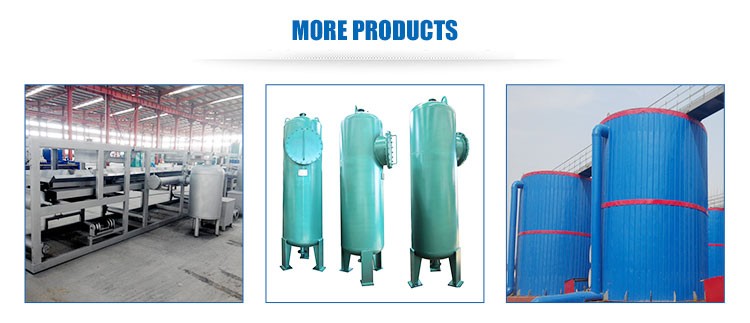
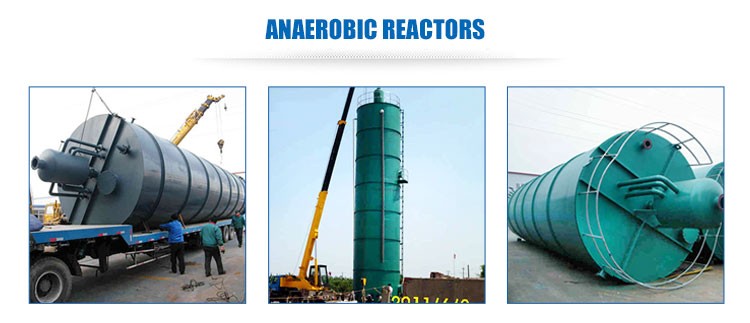
Pre-Sales Service
* Inquiry and consulting support.
* Sample testing support.
* View our Factory.
After-Sales Service
* Training how to instal the machine, training how to use the machine.
* Engineers available to service machinery overseas.