Grinder Crusher Crusher Granulator Granulator Blade Crusher Blade Strong Plastic Blade Low Noise Plastic Online Support 0.2 ABS
- $300.00 / 1 - 1 sets
$280.00 / >=2 sets - 1 set
- Nanjing Dete Machine Tool Co., Ltd.
- Jiangsu, China
- Mr amalia
PRODUCT DETAIL
Health status: | new | Package preview: | |
After-sales service: | online support | Mechanical test report: | if |
Origin: | Nanjing, Jiangsu Province, China | feature: | Efficient, safe and long life |
Video shipment inspection: | if | brand: | detection |
Supply capacity: | 5000 sets per year | payment terms: | L/C, Western Union, D/P, D/A, T/T, MoneyGram |
port: | Shanghai | Main selling points: | easy to operate |
Weight (kg): | 0.2 | Certification: | CE certification |
brand: | det | Applicable industries: | Hotels, Clothing Stores, Building Materials Stores, Manufacturing Plants, Machinery Repair Shops, Food and Beverage Plants, Farms, Restaurants, Home Use, Retail, Food Stores, Printing Shops, Construction, Energy and Mining, Food and Beverage Stores, Other, Advertising company |
size: | customer drawing | Material: | metal, metal |
Showroom location: | not any | Packaging Details: | wooden box |
Marketing Type: | New product | Warranty: | 1 year |
Spare Part Type: | paper shredder | Key words: | Case study of single-shaft, double-shaft and multi-shaft shredder |
After-sales service provided: | Video technical support | Application machine: | shredder shredder |
Product Description
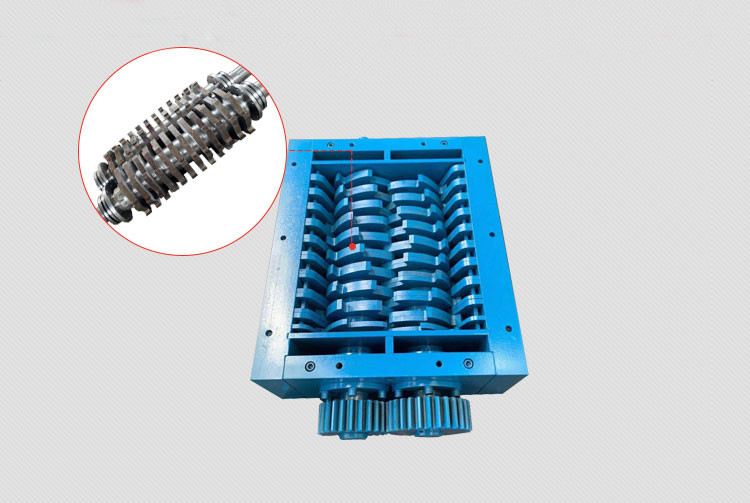
The shredder box is an important accessory on the shredder. The quality of the shredder blade directly affects the garbage processing cycle of the machine. According to the classification of shredders, shredder blades are divided into single-shaft shredder blades and shredder blades. Multi-shaft shredder blades. As an important shredding knife on the shredder.
According to the structure of the shredder, the shredder blade can be divided into single-shaft shredder blade and multi-shaft shredder blade. The multi-shaft shredder blade is a claw knife mounted on a twin-shaft or four-shaft shredder according to each company's design. Blades etc. are used for shredding, shredding and squeezing to reduce the size of the material. The shredder blade is used for shredding waste plastics, waste rubber, wood and other bulky wastes.
Commonly used shredder cutters have a diameter of 200mm-500mm and a thickness of 20mm-55mm. The inner hole is mostly hexagonal, and it can also be made into octagonal or circular (with keyway) according to customer needs. The shredder blades are quenched in salt bath furnaces and vacuum furnaces, which can make the hardness of various materials and specifications meet the requirements.
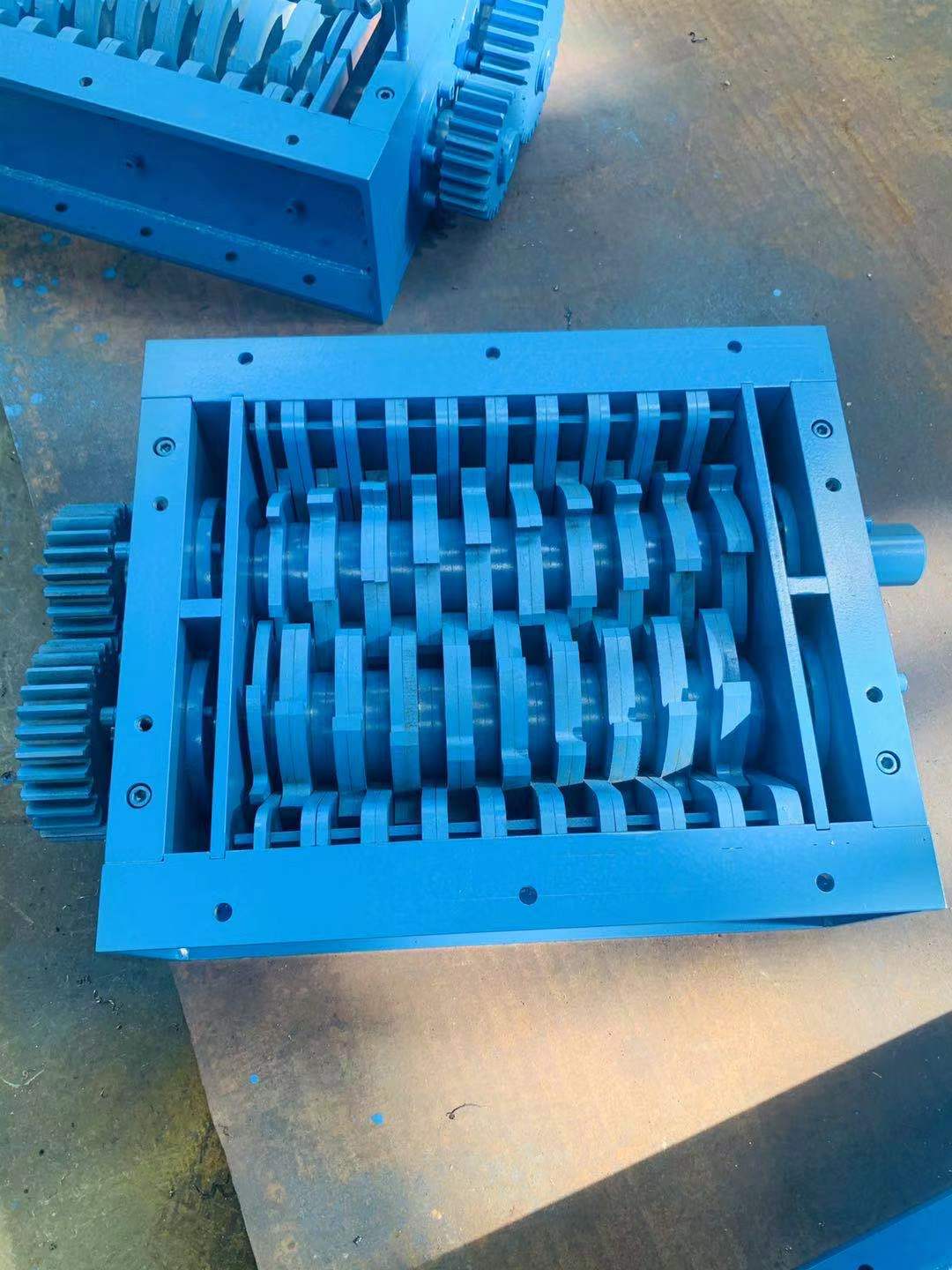
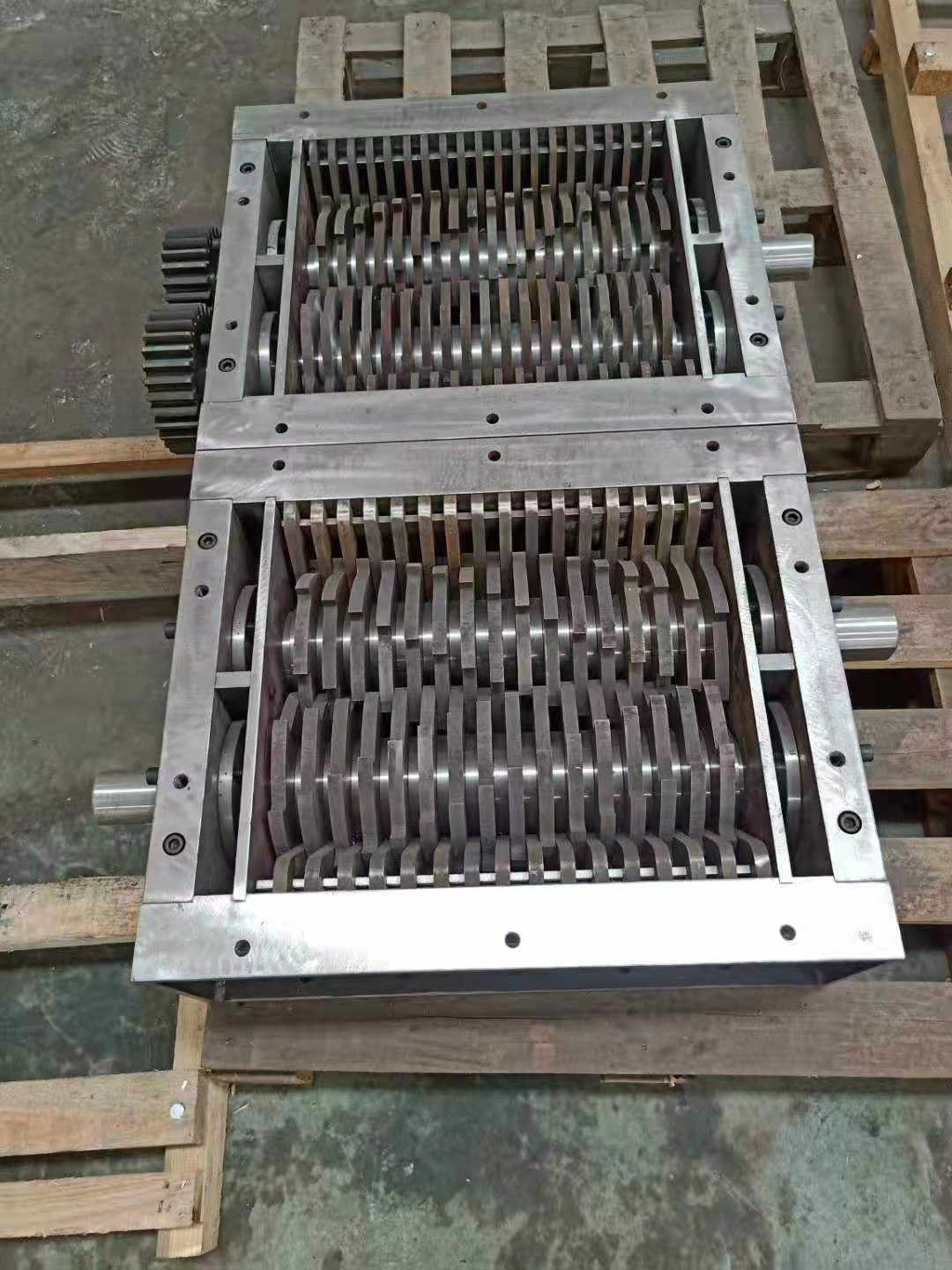
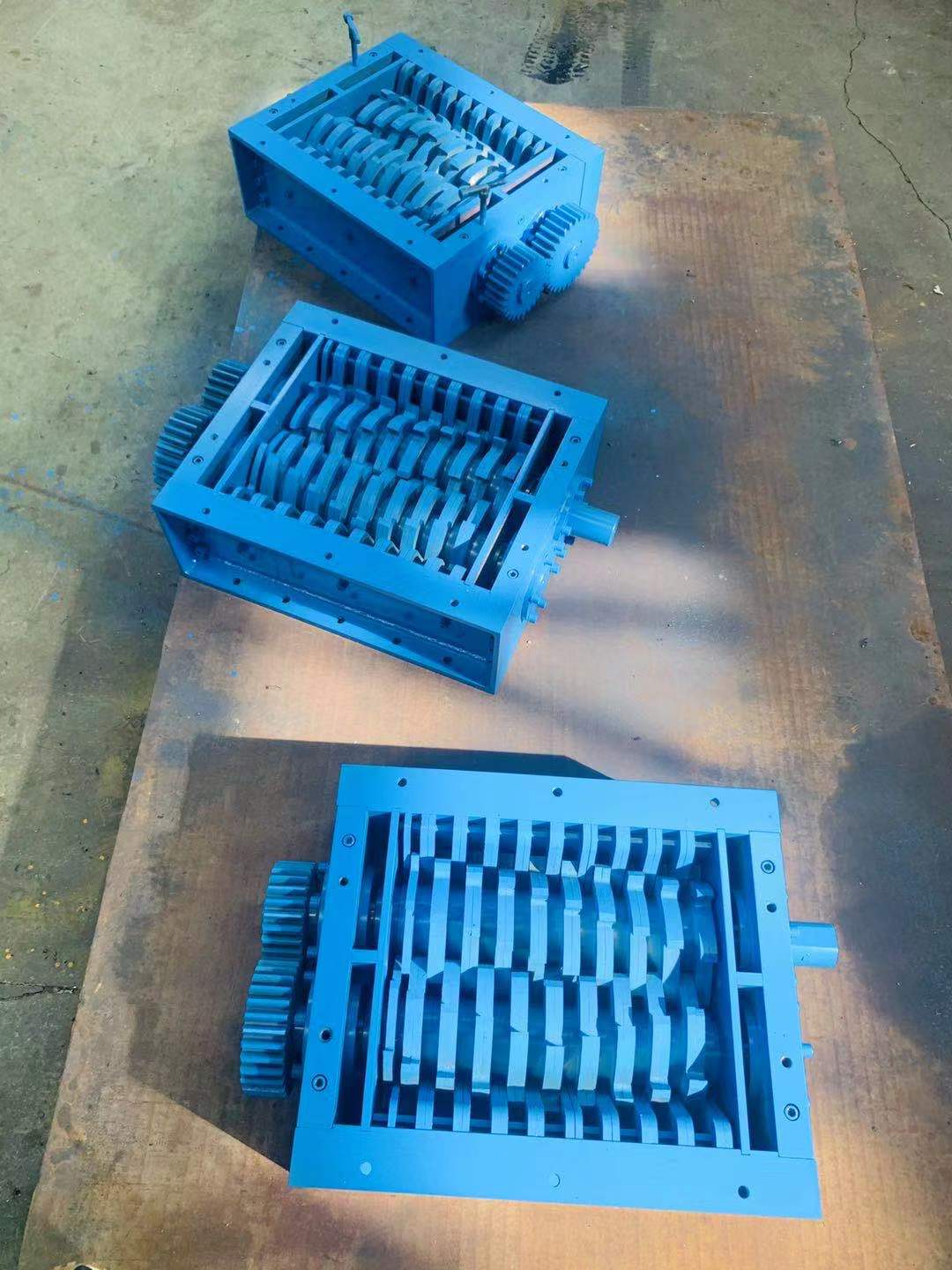
Product Details
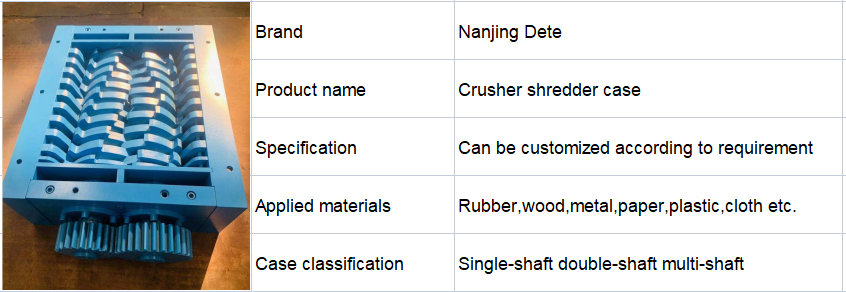
The material of the shredder blade is generally 9crsi, Cr12Mov, SKD-11, of which 9CrSi is alloy tool steel. This material has high hardness and good wear resistance, but is brittle. Suitable for rubber, fiber, paper and other materials. Soft waste, Cr12MoV and SKD-11 are cold work die steels. These two materials have similar properties, with strong wear resistance and impact resistance, suitable for broken wood, waste furniture and plastic with higher hardness.Choose different materials according to different processing objects.Plastic industry: 42CRMO, w5SICR.SKD-11.
Metal industry: 6CRW2SI, CR12Mov, LD, H13, SKD-11, D2. Wood industry: w5SICR, 6CRW2SI, SKH, SKD-11.
Heat treatment industry: HRC55-57.
Blade Specifications: Standard shredder blades are in stock, and non-standard knives can be customized according to customer drawings.Blade Features: The product has good wear resistance, strong impact resistance, and the cutting edge is durable and sharp.
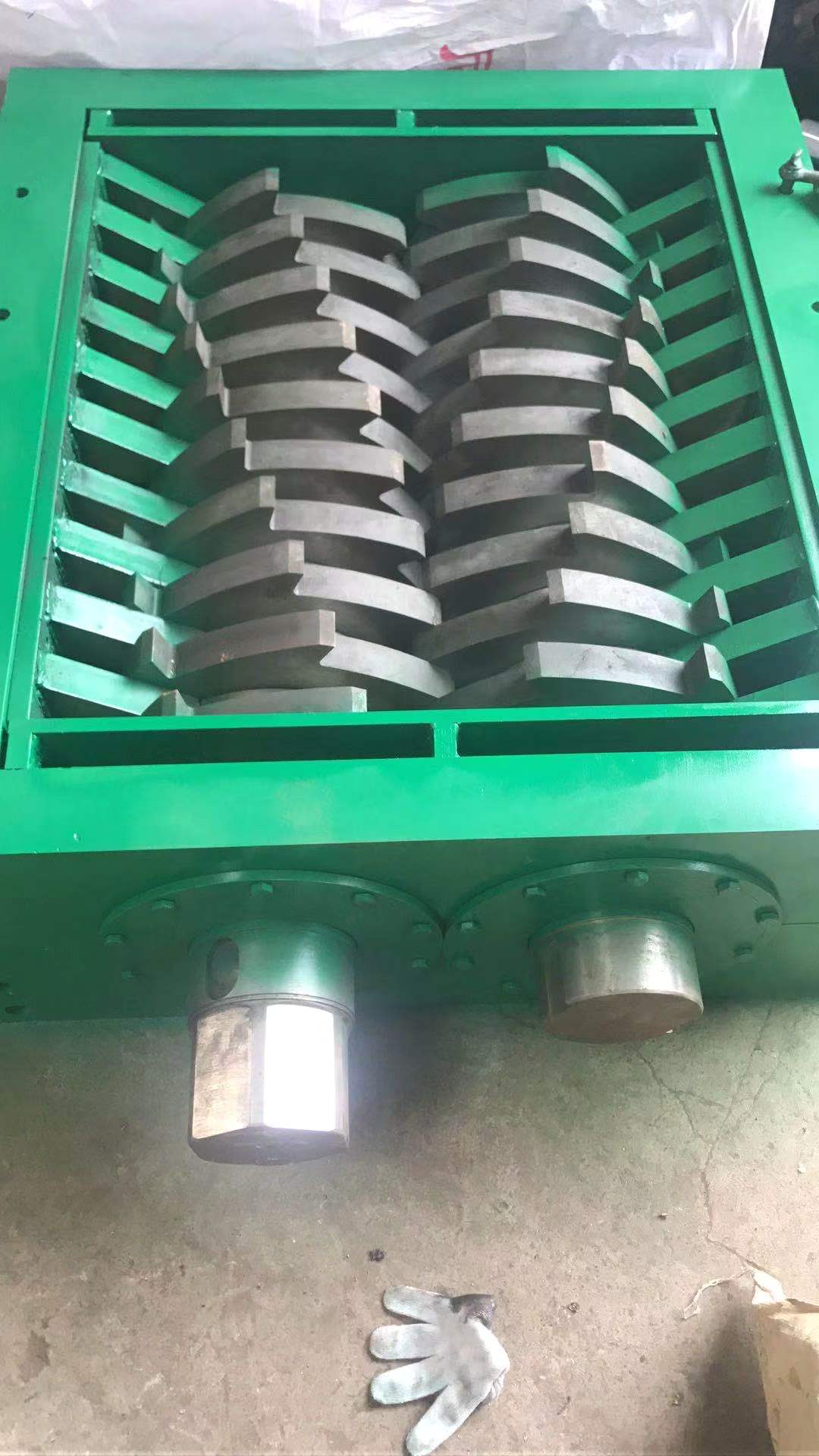
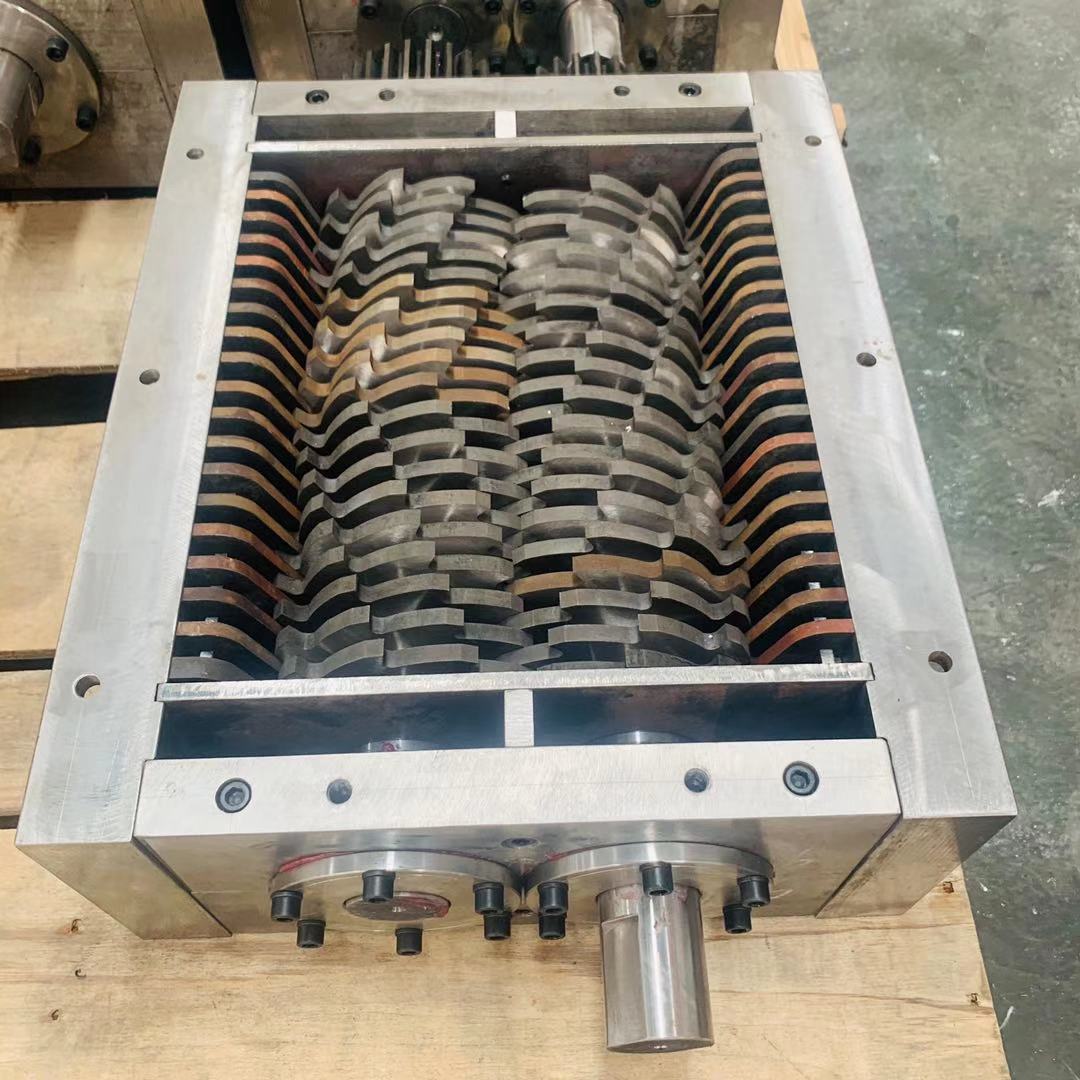
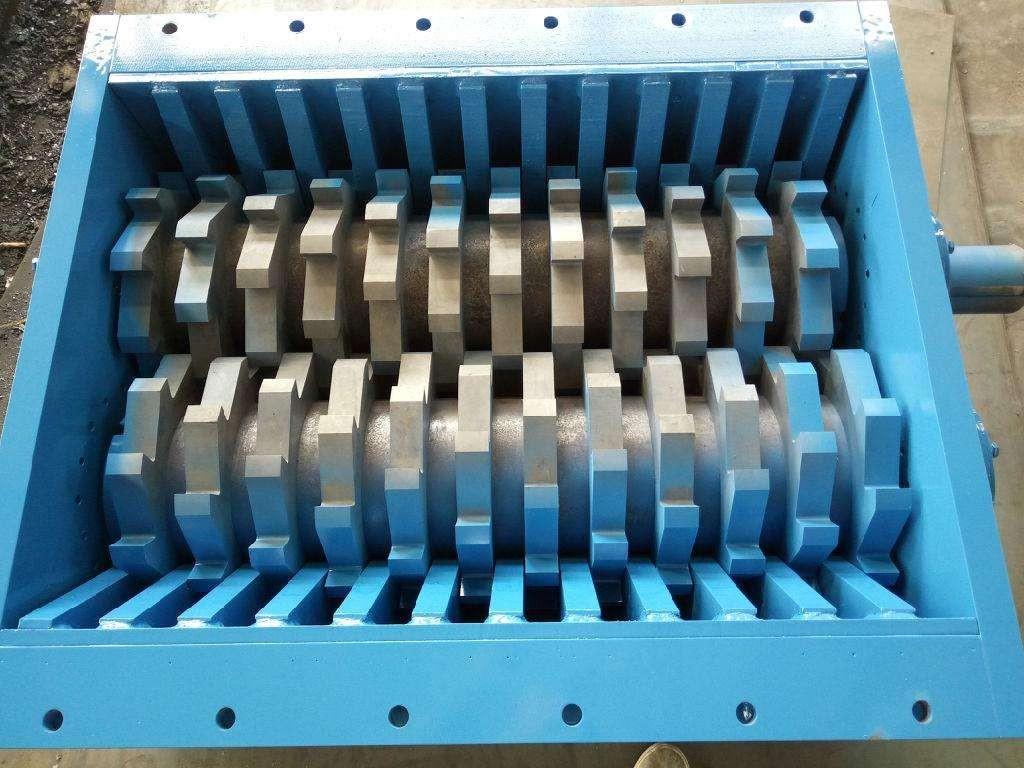
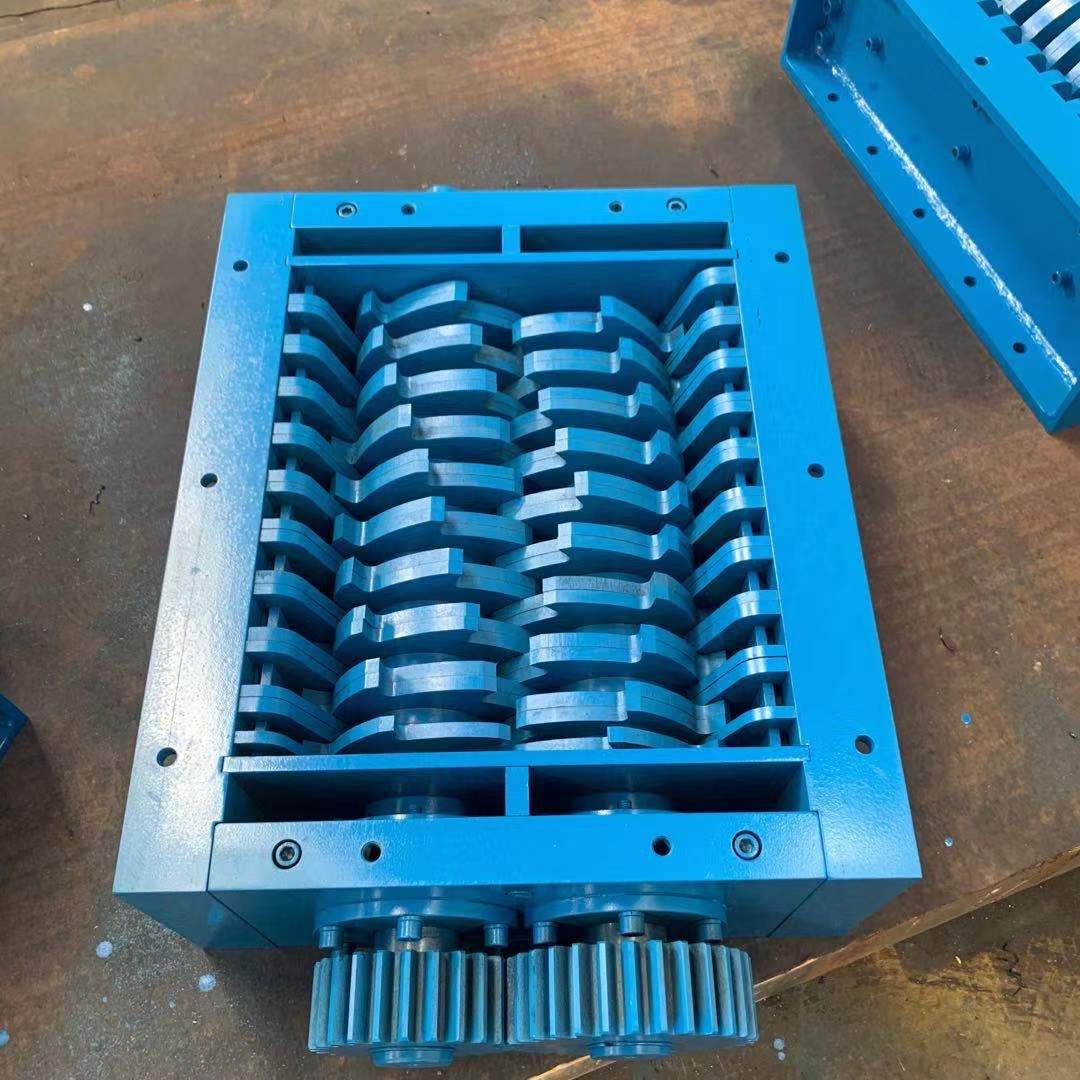
Manufacturing Technology
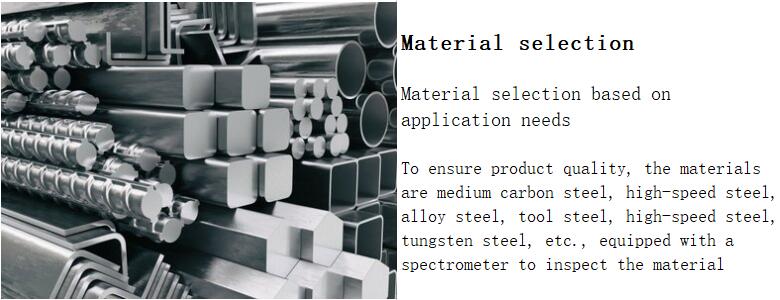
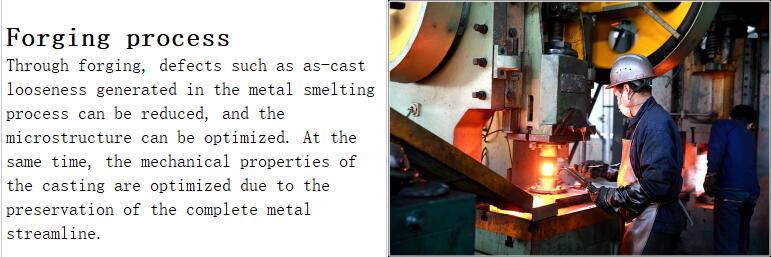
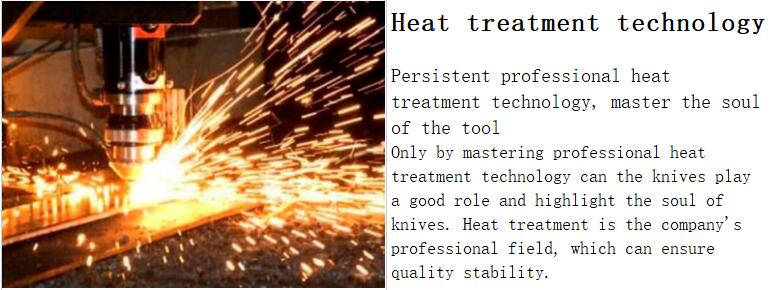
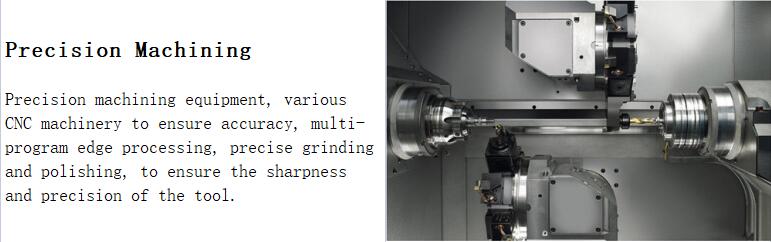
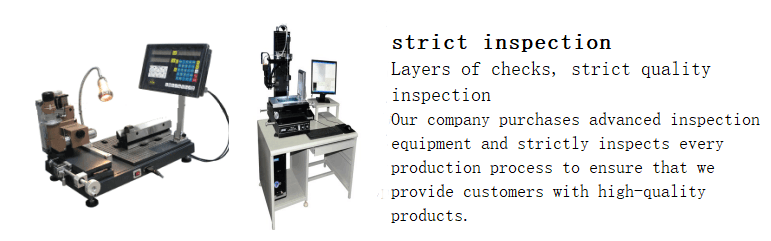
custom requirements: The standard blade only needs to provide the size, and the non-standard blade can be customized by providing the length, width, thickness, aperture and eye distance of the blade if the drawings and samples cannot be provided. Starting from cutting, we select the required materials strictly according to customer requirements. Every link from forging, rough machining, heat treatment, finishing to delivery, etc., is produced in strict accordance with technical requirements to ensure that customers can use qualified and quality-assured blades. The company has rich experience in the control of blade heat treatment hardness. Customers only need to inform us of the material of the crushed product, and we can recommend the most suitable blade hardness to ensure that the blade is in the best state in terms of toughness and wear resistance.
production process
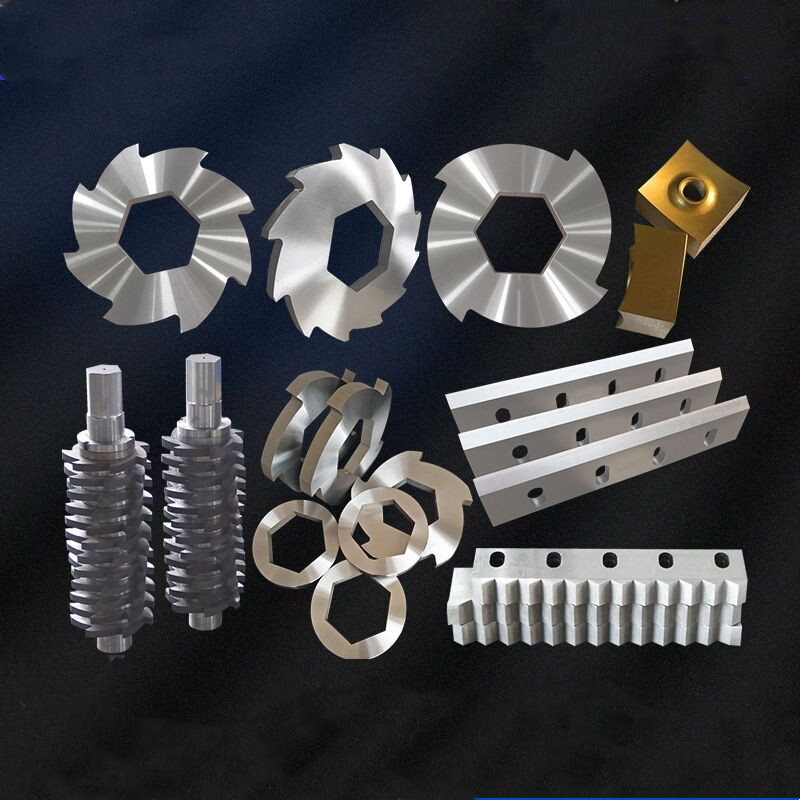
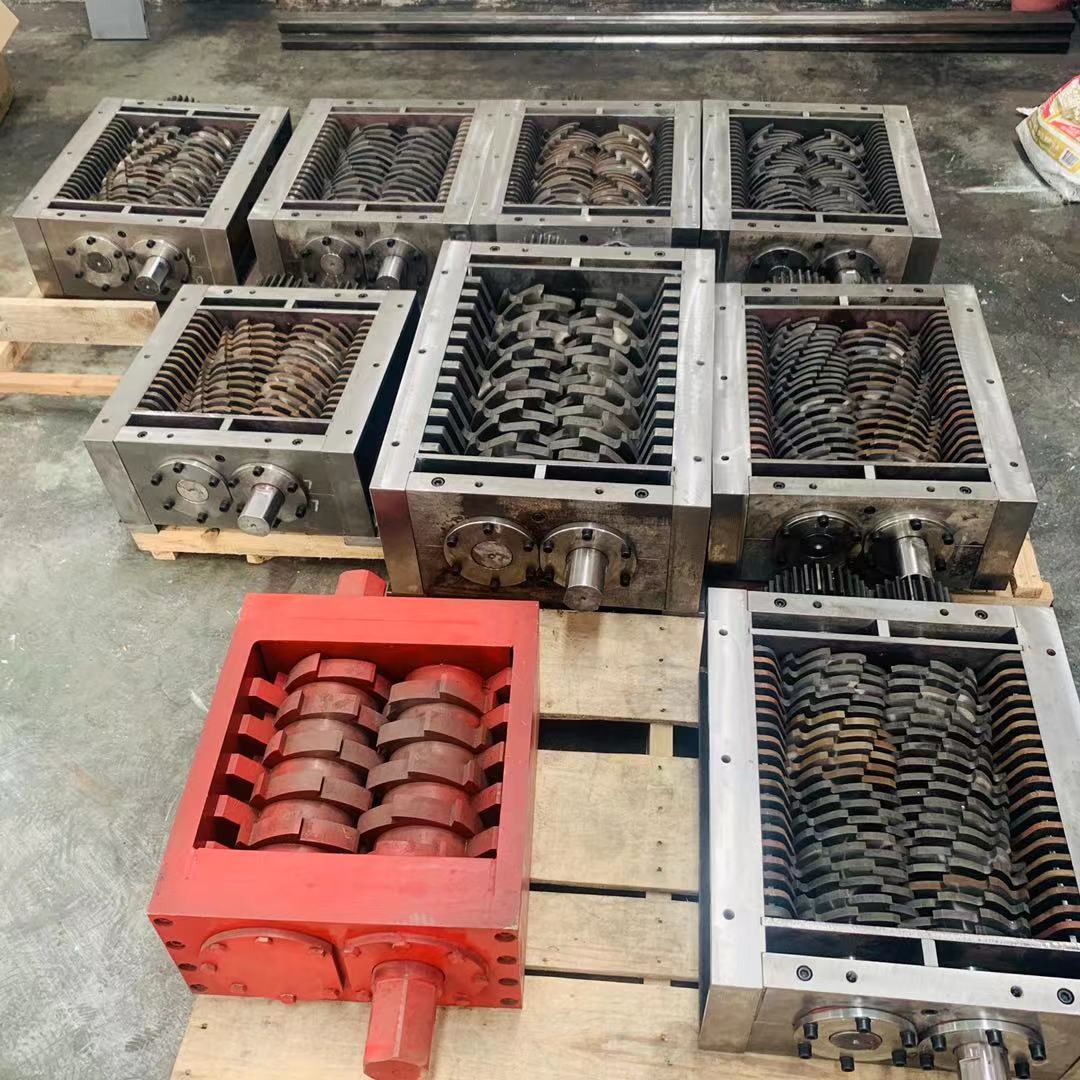
production process
◆1. Cutting material --- choose material according to customer's requirement.◆2. Forging--Forging is mainly to increase the density of the material.
◆3. Annealing - reduce the processing temperature.
◆4. Finishing - mainly to shape the material.
◆5. Inspection---Inspect whether the product is consistent with the drawing sample.
◆6. Quenching——Improve the corresponding hardness of molded products and materials.
◆7. Annealing——In order to increase the wear resistance of the product, long-time annealing treatment is necessary.
◆8. Quenching and tempering—mainly the parallelism of the quenching and tempering products to facilitate processing.
◆9. Coarse grinding—coarse grinding on each surface of the product.
◆10. Fine grinding - super fine grinding, mirror grinding, to improve the precision and parallelism of the product.
◆11. Inspection - Let unqualified products refuse to flow into the market.
◆12. Packaging--different packaging according to different products.
VIEW MORE
YOU MAY LIKE
Other Products
-
Dete small shredder metal waste single and double shaft shredder chassis plastic rubber shredder$99.00 - $300.00 / set
-
industrial iron ore crusher plant price$600.00 - $800.00 / set
-
Automatic Plastic Shredder Industrial Heavy Duty Single Shaft Steel Shredder Wood Shredder$1300.00 - $1600.00 / set